Go, Go, Lego Racer!
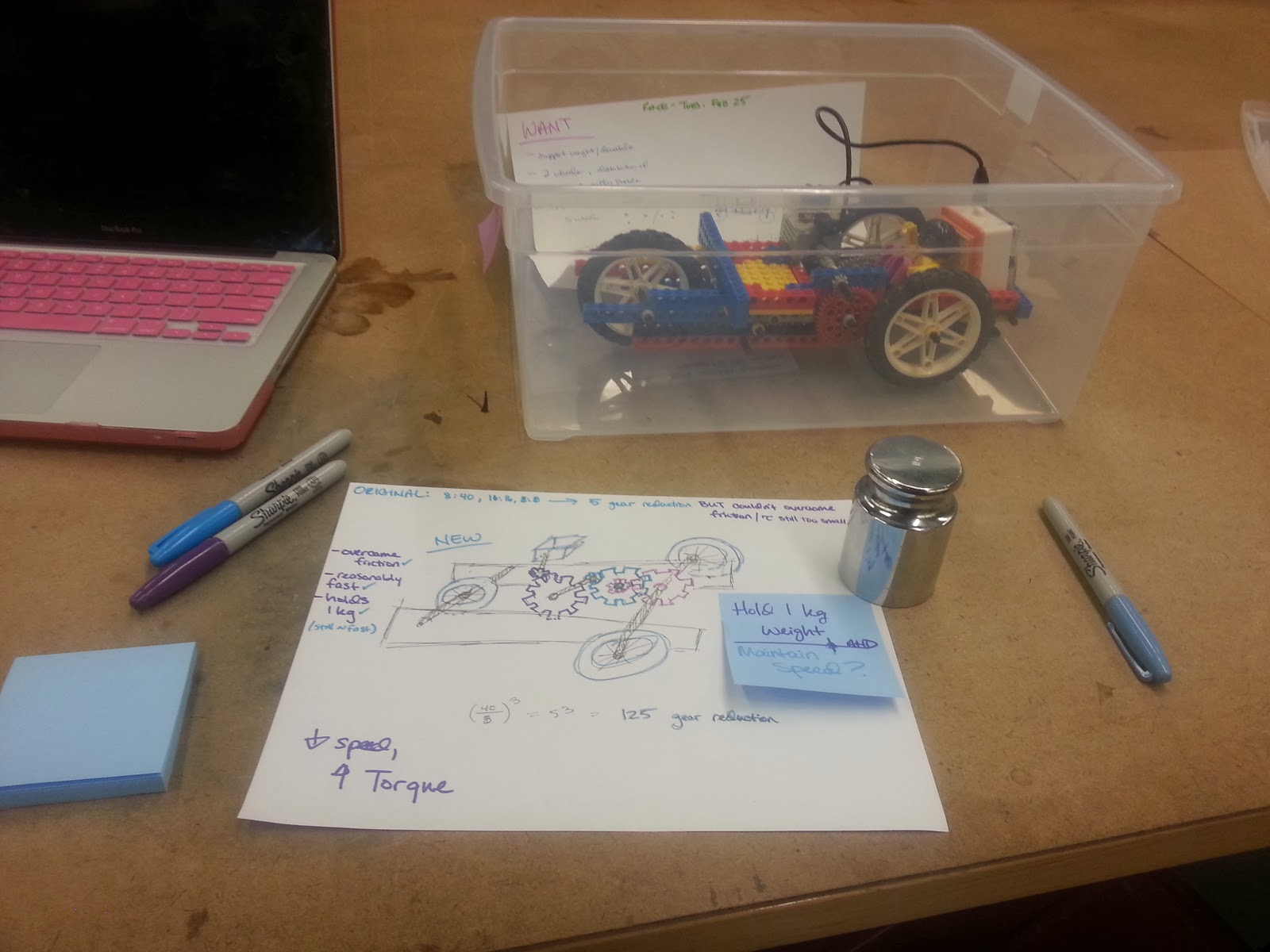
Objective: Discover the "magic" gear ratio to form a (relatively) fast Lego car that can carry a 1 kg weight in a race across a 4 m track. In our first iteration, we had trouble in getting our car to run. In our hands, the wheels would spin wonderfully but, once on the table, the wheels stalled. It then occurred to us what Professor Banzaert had said: "Torque is inversely proportional to speed." We finally figured out that, in order to produce enough power for the wheels -- or the torque -- to overcome the friction of the table (and later the 1 kilogram weight), we needed to decrease the speed. NOTE: Power is torque (τ) multiplied by angular velocity (ω) or P = τ∗ω. Also, τ =|F|∗|r|∗cosθ (F = mass of weight times gravitational acceleration 9.8 m/s^2), which translates for gears into |F|∗tanθ and ω=v/r (v = velocity and r = radius of the wheel). To decrease the speed, my partner and I had to increase the gear reduction ratio. Our first car had 3 pairs